Car Accident Lawyer Duluth helps their clients receive the compensation they are entitled to. They facilitate all communication with insurers and are skilled negotiators. They can help you understand the limitations of no-fault insurance systems, such as New York’s, and how serious injuries might allow a lawsuit against an at-fault driver.
Several types of insurance can cover car accident losses, including medical expenses and property damage. A lawyer can help you select the right policy for your needs and budget. They can also advise you on the types of compensation that you may be able to receive for your injuries and losses. These can include compensation for pain and suffering, lost wages, future earnings potential, and property loss.
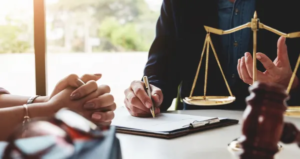
New York law requires all drivers to carry personal injury protection and property damage liability insurance. These policies pay for a driver’s own medical expenses, up to the limits of their policy. They also pay for the cost of repairing or replacing their vehicle after an accident. In addition, personal injury protection covers funeral costs and certain other out-of-pocket expenses.
In addition, most auto insurance policies provide uninsured/underinsured motorist coverage that can pay for a victim’s losses when the at-fault driver is either uninsured or does not have enough insurance to cover all of the crash-related costs. Under NY’s no-fault system, you will first file a claim with your own insurer and then seek additional compensation from the at-fault party’s insurance provider. Having uninsured/underinsured driver coverage can be particularly helpful when you have passengers in your vehicle at the time of the accident.
Car accidents can have many costs associated with them, from expensive medical bills and repairs to lost earnings and emotional trauma. An experienced NYC car accident lawyer can help you determine which damages are recoverable and help you calculate your total losses.
They can also assist you in completing all necessary insurance company forms, documenting your injuries and losses. Thorough documentation can strengthen your claim by demonstrating the severity of your injuries and the total cost of your damages. Documentation can also be used to support your claim for additional compensation, such as transportation costs to medical appointments or home care expenses.
Most car accident cases are resolved through a negotiated settlement, and an attorney can facilitate all communication with the insurance company to prevent you from accidentally compromising your case by admitting fault or accepting a low settlement offer. A lawyer can also evaluate any settlement offer to ensure that it adequately compensates you for your injuries and losses.
Uninsured motorists
The aftermath of a car accident can be very stressful. In addition to dealing with painful injuries, you may also face financial hardship due to unforeseen expenses like medical bills and vehicle repair or replacement costs. To help alleviate these issues, it is important to report the crash to the police and seek medical treatment as soon as possible. It is also vital to hire a qualified car accident lawyer, who can handle all aspects of your case and maximize your compensation.
A lawyer can be particularly helpful in cases involving uninsured motorists. In New York State, all drivers must have insurance coverage or face substantial fines, but sometimes people drive without insurance or do not carry enough coverage to pay for their losses in the event of a crash. Car insurance policies typically include a minimum of $50,000 in no-fault Personal Injury Protection (PIP) to cover medical/health expenses and lost wages, but these benefits are often not sufficient to pay for the full cost of an accident victim’s damages.
In some cases, a negligent driver will cause a collision with multiple vehicles and many injured victims. If this person has insufficient insurance coverage to pay for all the victims’ damages, their own policy will kick in to cover the remainder of the losses. This is why it is crucial to have uninsured motorist coverage as part of your auto insurance policy.
Additionally, if the at-fault driver leaves the scene of the accident and cannot be identified, having uninsured motorist coverage can still protect you. In this situation, the insurance company treats it as a hit-and-run accident and provides compensation from your own policy based on the limits of your UM coverage.
In cases where severe injuries lead to long-term loss of income, an experienced NYC car accident lawyer can work with economic experts to project these future losses and ensure that you receive adequate compensation for your loss. Non-economic damages, meanwhile, compensate you for your physical pain and emotional distress following the accident. These damages can be harder to quantify than medical or lost wage claims, but an experienced attorney can help you establish a fair value for your claim by considering the severity of your injuries and how they have affected your life.
Negligence
Establishing negligence in car accident cases is a key step when filing a claim for compensation. A skilled attorney can help victims understand how to prove these claims using evidence such as police reports, eyewitness testimony, camera footage, information obtained through the discovery process, and the expertise of experts.
The first step in establishing negligence is showing that the at-fault party had a duty to act in a certain way, for example, driving safely and following traffic laws. This is known as the plaintiff’s “duty of care.” The next step involves showing that the defendant breached this duty by not acting with reasonable care in the circumstances. Finally, the victim must demonstrate that this breach directly caused the injuries and damages they have suffered.
A variety of factors can cause drivers to violate their duty of care, including driving while distracted, speeding, and engaging in road rage behavior. These behaviors are called negligent acts and can result in catastrophic accidents that cause serious injuries to others on the road.
After an accident, the injured party must seek medical attention as soon as possible and make sure to document their injuries. This will provide proof of the severity of their injury and their related costs, which are essential in establishing damages in an auto negligence claim. Documentation can include medical bills and employment records that will help support these claim elements.
It is also vital to exchange driver and insurance information with the other motorist involved in the crash. Additionally, if it is safe to do so, call the police, as they will create an official report of the accident that can be used as a piece of evidence in a negligence claim.
A car accident lawyer can assess the viability of a negligence claim, assist with preparing relevant documents and evidence, and negotiate with insurers on behalf of the client. In addition, many attorneys work on a contingency fee basis, meaning they only get paid if the client wins their case. This alignment of interests can significantly increase the odds of a successful outcome.
Damages
When a person suffers injuries in a car accident, they may also need financial compensation. This is known as “damages.” These damages can help cover expenses related to medical care, property damage, and lost wages. They can also compensate for non-economic losses like emotional pain and suffering. However, no amount of money can fully make up for the physical and psychological toll that an injury takes on a person. That’s why it’s important for a victim to find a good car accident lawyer to help them receive the maximum amount of compensation possible.
It’s also important to seek medical attention as soon as possible after a crash. Not only is this the best thing to do for your health, but it will also strengthen your claim by establishing causation. This is because some injuries, such as internal bleeding and concussions, don’t reveal themselves until days or even weeks after the incident. Documenting these injuries will prove that your injuries were caused by the accident and will serve as solid evidence to support your claims in court.
Additionally, it’s important to bring all relevant documentation related to your case to your initial consultation with a car accident lawyer. This could include repair estimates from auto body shops, notes taken at the scene, and other important information. It’s also a good idea to bring copies of any documents from your insurance provider, including the police report. Finally, if your vehicle was damaged in the accident, you should also bring the Kelley Blue Book value of your vehicle.
A car accident lawyer will review this paperwork and assess the adequacy of coverage to cover your potential damages. They’ll also calculate the total cost of your damages, taking into account past, present, and foreseeable future expenses.
It’s important to choose a car accident attorney who has a history of handling similar cases in your area. This will give them a deep understanding of relevant laws and regulations, allowing them to negotiate better settlements and represent you in court more effectively. They should also be willing to keep you updated on the status of your case on a regular basis.